Swedwood Karelia’s FSC certificate has been suspended. The suspension affects 295,348 hectares in the Russian Karelia region.
FSC’s annual audit report for Swedwood Karelia LLC reveals six Major Corrective Action Requests (CARs) and 11 Minor CARs. Because five Major CARs were still open, the Audit Report led to the immediate suspension of Swedwood Karelia’s Forest Management certification. This suspension affects 295,348 hectares in the Russian Karelia region. The company’s Chain-of-Custody certification is not affected. Swedwood Karelia is a subsidiary of IKEA, the worldwide home furnishing company. FSC welcomes the fact that both Swedwood and IKEA have committed to taking immediate action to correct the CARs. In a statement, Swedwood confirmed its commitment: “We take our responsibility for the forests and the people who work there very seriously and we appreciate that correcting the deviations will improve the way we manage the forest in Karelia. IKEA is committed to responsible forest management and to the principles of the FSC. Our lease in Karelia has been FSC certified since 2006 and we believe that a reinstated FSC certificate will continue to be the best protection for natural values in the logging areas.”
All posts by IFI_admin
North American lumber industry looking solid again
Demand expected to drive further recovery over the next two years – Housing demand in the United States was a key reason for the lumber market crash in 2009. As U.S. housing, and more importantly housing starts, continue to recover, the North American softwood lumber industry is expected to see both demand and price increases. This is according to a new report from the Rabobank Food & Agribusiness Research and Advisory (FAR) group, titled “North American Softwood Lumber: Industry Outlook Solid, But Not Out of The Woods Yet.”
As indicated in the title, the bank’s current outlook is very optimistic but notes a number of potential challenges. “U.S. lumber production and imports are constrained at the moment,” noted Rabobank analyst James De Jong, the report’s author. “This limited supply, in addition to overall economic recovery, is the reason we expect to see softwood lumber prices increase 10 to 15 percent over the next two years.” The report goes on to outline the biggest challenges for the industry. “The biggest challenges we see are the headwinds in the Chinese economy and the U.S. housing market transition,” notes De Jong. “The housing market in particular is still in a significant transition. The adjustment from an investor-led recovery to one driven by ‘real’ homebuyers will create bumps in the road but our expectation is that this will affect, but not derail, the lumber recovery. ” The full report is available exclusively to clients of Rabobank and to media upon request.
CONTACTS: FAR Report Requests/Media Inquiries Lynne Burns Rabobank North America Wholesale D: 212-808-2581 Lynne.Burns@rabobank.com Jessup Wiley Rabobank, N.A. D: 559-353-4608 North American lumber industry looking solid again
Chugoku Lumber reduces beam prices by 2,000 yen ($19.6)
Chugoku Lumber, the largest Douglas fir lumber manufacturer in Japan, decided to reduce dry beam lumber prices by 2,000 yen ($19.6) per cubic metre after lumber market has been weak since April after the consumption tax was increased by 3%. Movement of structural materials has been slowing since last January, ITTO reports.
The prices peaked in January and the movement got worse after April. Competing laminated lumber prices are also weakening. Douglas fir log export prices dropped for two straight months of April and May.
Tigercat breaks ground for new manufacturing facility
Tigercat® is pleased to announce it has officially broken ground for a new $12 million, 127,000 square foot manufacturing facility in Paris, Ontario, Canada, located approximately 100 km southwest of Toronto.
Several hundred employees, community officials, Tigercat partners and supporters attended an official ground breaking ceremony last week to mark the start of construction and celebrate the companies continued growth. Tigercat also announced the purchase of an existing 66,000 square-foot plant in Kitchener, Ontario. “This is a significant milestone for our company,” states President, Tony Iarocci, who was Tigercat’s first employee when the company started in 1992. Tigercat is one of the few remaining heavy equipment manufacturers in a region that once was at the heart of the industry. Tigercat currently has seven southern Ontario locations, a large parts distribution and training centre in Georgia, a sales and distribution facility in Sweden and a dealer network that spans the globe, covering the forestry regions of North America, South America, Australasia, southern Africa, Europe and Russia. The new building will be located on the same property as the current Paris, Ontario facility, on a previously vacant lot at the northwest corner. The new plant will initially focus on swing machines and cut-to-length attachments including the 200 series material handlers and the 800 series track feller bunchers, harvesters and shovel loggers. Iarocci explains that the new plants do not tell the whole story of the scope or capacity of the ever-growing Tigercat. “These two projects will increase the company’s manufacturing footprint by 20%. The space is urgently needed for existing demand and future growth. We already have over 1,200 employees and 200 or 300 more subcontractors.” Vicano, the construction company hired for the project, will be including numerous crane lanes and flexible assembly lines along with a large office space for an engineering group allowing the building to be flexible for future projects.
About Tigercat
Tigercat Industries designs and manufactures premium quality forestry and off-road equipment with manufacturing facilities in Canada and worldwide distribution. The diverse product range includes complete full-tree and cut-to-length harvesting systems, a growing line of land clearing and vegetation management equipment and specialized off-road industrial and material handling machinery.
Contacts:
Samantha Paul
Marketing Specialist Tigercat Industries Inc.
Tel: 519-753-1539 ext. 4279
Email: spaul@tigercat.com
John Deere Introduces the M-Series Tracked Feller Bunchers and Harvesters
Three years in the making and backed by over a half-century of experience in the woods, the John Deere M-Series Tracked Feller Bunchers and Tracked Harvesters are officially making their debut. The latest additions to the John Deere family of tracked forestry machines include the 800M and 800MH-Series Reduced Tail Swing, setting a new standard in midsize machines, along with the 900M and 900MH-Series that improve upon John Deere’s industry-leading large-size machines.To develop the M-Series Tracked Feller Bunchers and Tracked Harvesters, John Deere enlisted loggers from around the world to form a Customer Advocate Group (CAG). The CAG provided real-world insights on what they need in a machine to be successful. Inspired by their feedback and validated by thousands of hours of testing in every day conditions, John Deere listened and responded with machines that change the game in terms of uptime and productivity. “When we designed our new midsize and large-size machines, we relied on the input of the people who are in the machines every day – our customers,” said Cliff Caudill, Manager, Product Marketing, John Deere Construction & Forestry. “After collecting invaluable customer input, we spent over 11,000 hours testing the machines until we got them exactly right. The result is a new fleet of machines that redefine the meanings of uptime, productivity and low daily operating costs.” The M-Series machines are built for the way loggers work, and the proof is in their feedback:
- “It’s so important to get customer input into a product because we’re the ones who spend our lives in the equipment. These machines are very well built, and they represent pretty much everything we asked Deere to build.” – Mark Maenpaa, K&M Logging, Thunder Bay Canada
- “John Deere addressed everything we asked them for. What’s not to like? The stability, the visibility, the serviceability. Hats off to them for building machines that fit many different applications. They’ve done a great job.” – Brent Day, William A. Day Jr. & Sons, Porter Maine
- “I didn’t realize how committed John Deere is to its customers until I was involved in the Customer Advocate Group. It really opened my eyes to how they are as passionate about logging as we are.” – Rick Cuneen, Plantation Harvesting, Myrtleford, Victoria Australia
800M- and 800MH-Series machines share many common components – including the engine, undercarriage, booms and cab – with their 900M- and 900MH-Series counterparts, simplifying maintenance and repairs when needed. Maximize Productivity Rapid Cycle System (RCS) combines automated felling-head arm cycling with simple boom control, dramatically reducing operator fatigue while increasing efficiency and productivity. RCS can be tailored to individual skill levels and specific harvesting conditions, from large single-tree harvesting to high-speed, multistem cutting. An added benefit for operators is its selectable operation, which allows them to engage and disengage RCS with a single touch of a button. Multiple RCS settings can also be saved according to individual operator preferences based on skill levels. RCS is standard on all 800M- and 800MH-Series machines and as an option on the 900M and 900MH-Series. Operate in Comfort The new operator station on all M-Series machines was designed by loggers for loggers. It’s roomier and more comfortable, with ergonomically designed controls. Fully adjustable armrests provide fingertip control of all machine functions, and an air-conditioned seat provides exceptional daylong comfort in the climate-controlled cab. Floor-to-celling front and side windows plus an overhead skylight provide 44 percent more visibility, providing an outstanding view of the cutting area. Increase Uptime All machines feature John Deere’s field-proven boom design from the 900M- and 900MH-Series models. All booms are strong and robust with thick plates and large pins and bushings to ensure long life. Additional uptime increasing features include:
- A through-nose harvester head plumbing option that routes hoses up and out of harm’s way to extend hose life.
- An optional undercarriage-mounted toolbox that provides convenient storage for tools, additional saw bars and other spare parts, minimizing trips to a service truck.
- 800M fuel tank capacity has been increased by 50 percent to extend intervals between fill-ups, allowing loggers to run up to 24 hours without refueling.
- John Deere ForestSightTM and Ultimate Uptime are also available as an option on all M-Series machines. This integrated suite of technology solutions brings the machine, technology and the dealer together to help loggers better manage their equipment and operations with fast, accurate remote diagnostics, rapid service response and on-demand dealer support.
John Deere’s 800M- and 800MH- Series and 900M- and 900MH- Series family of Tracked Forestry machines are now available in North America. To learn more, view product features and hear real customer feedback, visit www.JohnDeere.com/GameChangers. Worldwide Construction & Forestry Division Mailing: P.O. Box 8806 Moline, IL 61266-8806 Media Contact: Caitlin Haskins IMRE Phone: 410-821-8220 E-mail: caitlinh@imre.com
Tigercat – New Product Support Representative North Carolina
Tigercat is pleased to announce that Aaron Piper has joined the Tigercat product support team.
Based in Sunbury, North Carolina, Aaron will focus on providing after-sales technical and commercial support to Tigercat’s customer base in the southeastern United States. Aaron will work closely with Tigercat dealers and prospective customers to further grow Tigercat’s market share in this territory.Aaron has worked in the construction and forestry industry for 17 years. He started in the industry with Komatsu as a resident Field Technician, primarily working on excavators. From there Aaron went to work for a utility contractor providing product support to the entire equipment fleet. Aaron has also worked as a Field Technician for John Deere then moved up to the role of Service Manager. Aaron brings great experience and technical skills to Tigercat. He is very excited to have the opportunity to be a part of the Tigercat team and looks forward to meeting and working with the dealer network and end users. Aaron Piper, Product Support Representative
– See more at: http://www.tigercat.com/new-product-support-representative-in-north-carolina/#sthash.uwQeA2ur.dpuf
Demo International® Returns to the West Coast
Back in October 2014, the Canadian Woodlands Forum (CWF) proudly announced that DEMO International® was returning to the west coast and would be held in Maple Ridge, British Columbia, Canada, on September 22-24, 2016. The Faculty of Forestry at the University of British Columbia will host the event at their Malcolm Knapp Research Forest located within an hour’s drive east of downtown Vancouver. The Knapp Forest is truly a multiple use research forest, providing an ideal location and forested venue for an event of the scope of DEMO International® 2016.This world class event, occurring only every four years, will mark the 13th edition of DEMO International®. During the course of its 49 year history, DEMO International® has evolved into one of North America’s largest and unique outdoor equipment shows. The “all live and in-woods” equipment show will feature the latest technologies in equipment, products and services covering all aspects of woodlands operations, and will attract individuals interested in forestry from around the world. The Canadian Woodlands Forum will work once again with Master Promotions Ltd., and along with our host with the Faculty of Forestry at the Knapp Forest, will provide for a great team and event in 2016. Plans are well underway at the Malcolm Knapp Research Forest in designing a show site that meets the highest of standards and expectations. We are now ready to launch the site selection process for interested exhibitors, providing suppliers an opportunity to visit the forest and choose their site. Please review the attached notice and complete the form to ensure that you are part of the process. If you have any immediate questions, please feel free to contact Mark Cusack with Master Promotions Ltd. or any of the undersigned. We look forward to working with you towards a successful event in 2016!
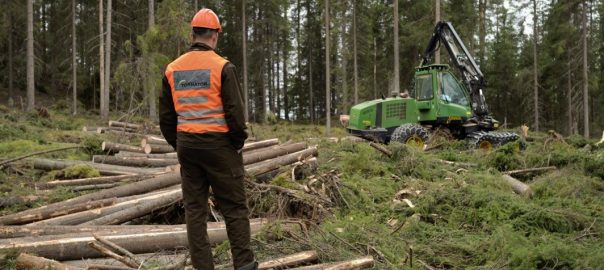
Tornator Oyj AGM elects Board of Directors
The Annual General Meeting of Tornator Oyj discharged the members of the Board of Directors as well as the CEO from liability for the financial year 2014. Elected on the Board were Mikko Koivusalo, Erkko Ryynänen, Jari Suominen, Esko Torsti and Jari Puhakka. Continuing as authorised public accountants will be Deloitte & Touche Oy with Jukka Vattulainen as principal auditor.
The Board of Directors elected Esko Torsti to continue as Chairman and Mikko Koivusalo as Vice Chairman of the Board. The Board elected among itself Mikko Koivusalo as Chairman and Erkko Ryynänen and Jari Puhakka as members of the Oversight Committee. Esko Torsti and Mikko Koivusalo were elected as members of the Remuneration Committee. Tornator core business is wood production and the sale of cutting rights.
See more at: http://www.lesprom.com/en/news/Tornator_Oyj_AGM_elects_Board_of_Directors_67300/#sthash.AOe8h1Vt.dpuf
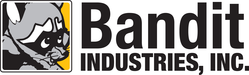
Bandit Industries, Inc. completes fourth plant expansion in nine months
Bandit Industries recently completed the forth plant expansion in nine months to keep up with increasing demand for its equipment. All the plant expansions add space for additional employees and increasing production at the company’s Mid-Michigan facility. Bandit moved into a new rebuild facility in October of 2014, increasing its capacity for rebuilding used machines. The move also freed up construction space in the forestry mower and Beast buildings, allowing the forestry mower area to double its production and allowing the Beast recycler line to increase production by 25 percent. A new electronics facility was finished in November 2014, allowing for increased production of electronic control panels harnesses used on all Bandit equipment. The new facility is now building all of the new control panels and proportional drives that are now featured on all of Bandit’s Tier 4 engine options. “In February of this year, we moved into a new facility to build drum chipper heads for our hand-fed chippers, whole tree chippers and Beast recyclers, along with the rotors for our forestry mower lines,” said Jerry Morey, president of Bandit Industries. “The new facility freed up production areas in our hand-fed drum chipper area, which is allowing us to increase production in that area by 50 percent.” On April 1, Bandit Industries moved into an expansion of its whole tree manufacturing facility, increasing production of its whole tree chippers by 50 percent, Morey added. “These four expansions have allowed us to add 80 full-time employees and add much-needed production,” Morey said. “Surging demand for our products over the past two years has increased lead times longer than I like, and at times has cost us orders. The additional production capacity will reduce lead times by the end of the second quarter,” Morey said. Learn more about Bandit’s lineup of wood processing equipment by visiting www.banditchippers.com or by calling 1-800-952-0178.
100 FREE LIGNA Tickets with IFI Magazine
If you would like to include the free tickets in your next digital mail out please feel free to use the following code http://www.ligna.de/promo?ut4y5